
This is comparable to the coordinate system at the origin of a space in 3D modeling programs. When measuring and defining a part, the geometry exists in a conceptual space called the Datum Reference Frame (DRF). Using specific tools such as digital micrometers and calipers, height gauges, surface plates, dial indicators, and a coordinate measuring machine (CMM) are important to tolerancing practice.
#OPENSCAD OVAL HOW TO#
The standards do not only pertain to designers and engineers but also to quality inspectors by informing them how to measure the dimensions and tolerances. When installing repeated elements such as a perforated hole pattern, first position the pattern and then specify interrelated distances rather than referencing elements to a fixed edge or plane of the part.
#OPENSCAD OVAL PLUS#
If we create a chain link where each hole has a 0.1 mm plus tolerance and each shaft a 0.1 mm negative tolerance, that means we will still accept a 20 mm length difference at 100 links. For example, when a part comes out with all dimensions at their maximum allowed value, does it still meet overall requirements such as product weight and wall thicknesses? This is called the Maximum Material Condition (MMC), while its counterpart is the Least Material Condition (LMC). The manufacturer then only needs to look up the basis table for hole features to derive the exact tolerance value.īesides individual tolerances, engineers must take into account system-level effects. The symbol 40H11, for example, means a 40 mm diameter hole with a loose running fit. In the metric system, there are International Tolerance (IT) grades that can also be used to specify tolerances by means of symbols. The art of tolerancing means to specify just the right variations for all specific design features in order to maximize product approval rate within the limits of the manufacturing processes and depending on the part’s visual and functional purpose. As a result, multiple departments are able to work more in parallel because they have a shared vision and language for what they want to achieve. When performed well, GD&T even allows statistical process control (SPC), reducing product reject rates, assembly failures, and the effort needed for quality control, saving organizations substantial resources. It also provides a communication tool with manufacturing vendors, customers, as well as quality inspectors. Or, when drilling a hole, it makes the most sense to tolerance it in terms of alignment to other features.ĭescribing product geometry related to its intended functionality and manufacturing approach is ultimately simpler than having to describe everything in linear dimensions. This will define two planes spaced apart, that the center plane of the feature must fall within. Like a vector or formula, it is not the actual object but a representation of it.įor example, a feature standing at 90 degrees to a base surface can be toleranced on its perpendicularity to that surface. The most important benefit of GD&T is that the system describes the design intent rather than the resulting geometry itself. GD&T is the system that allows developers and inspectors to optimize functionality without increasing cost. Tightening tolerances by a factor two can raise the costs twofold or even more, due to higher reject rates and tooling changes. All relevant fits and features need to be specified in a way that impacts the manufacturing process and its related investments the least, while still guaranteeing functionality. With functional assemblies, multi-part products, or parts with complex functionality, it is crucial that all components work well together.

It concerns mostly the overall geometry of the product, while other standards describe specific features such as surface roughness, texture, and screw threads.
#OPENSCAD OVAL ISO#
Once proven as a better operational method, the new system became a military standard in the 1950s.Ĭurrently, the GD&T standard is defined by the American Society of Mechanical Engineers ( ASME Y14.5-2018) for the USA and ISO 1101-2017 for the rest of the world. Driven by the need for cost-effective manufacturing and meeting deadlines, he worked out a new system through several publications.
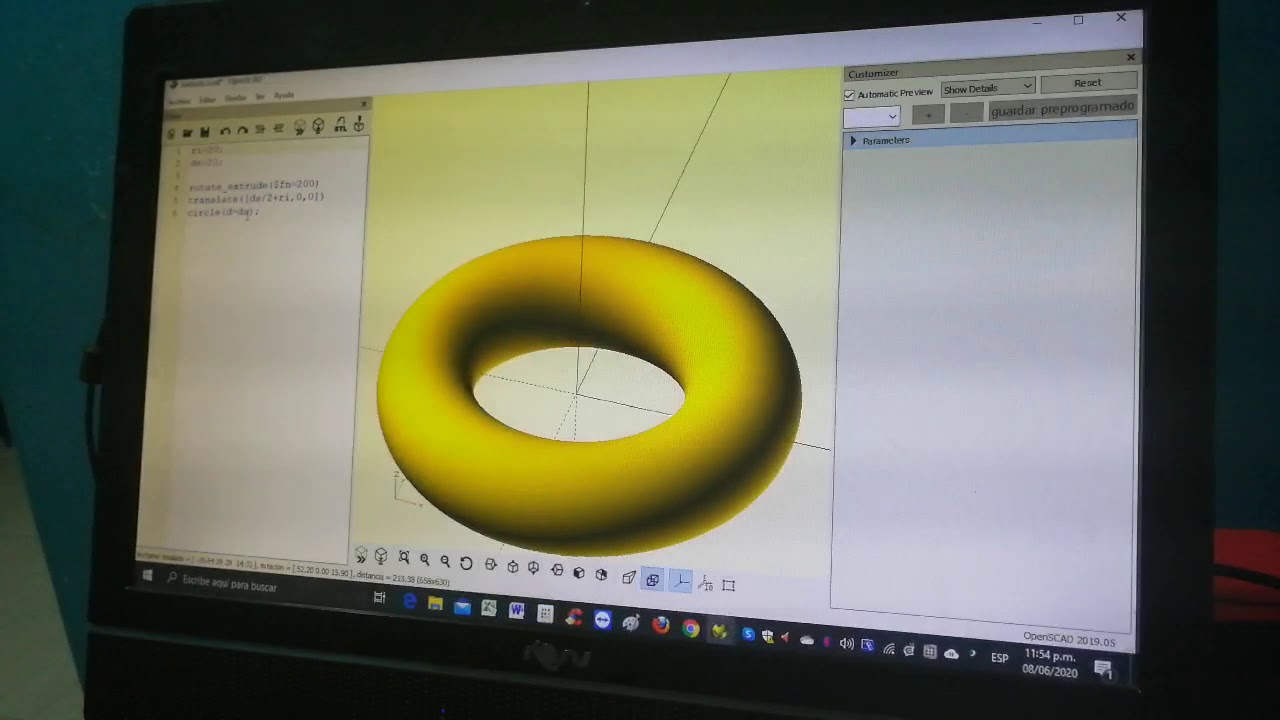
Stanley Parker, an engineer who was developing naval weapons during World War II, noticed this failure in 1940. X-Y tolerancing leaves a zone in which inspection would have produced a false negative because while the hole is not within the X-Y square, it would fall within the circumscribed circle. For example, when drilling a mounting hole, the hole had to be within a specified X-Y area.Īn accurate tolerancing specification, however, would define the position of the hole in relation to the intended position, the accepted area being a circle. Before GD&T, manufacturing features were specified by X-Y areas.
